Plastic Rapid Prototyping: Elevating Businesses with Precision and Speed
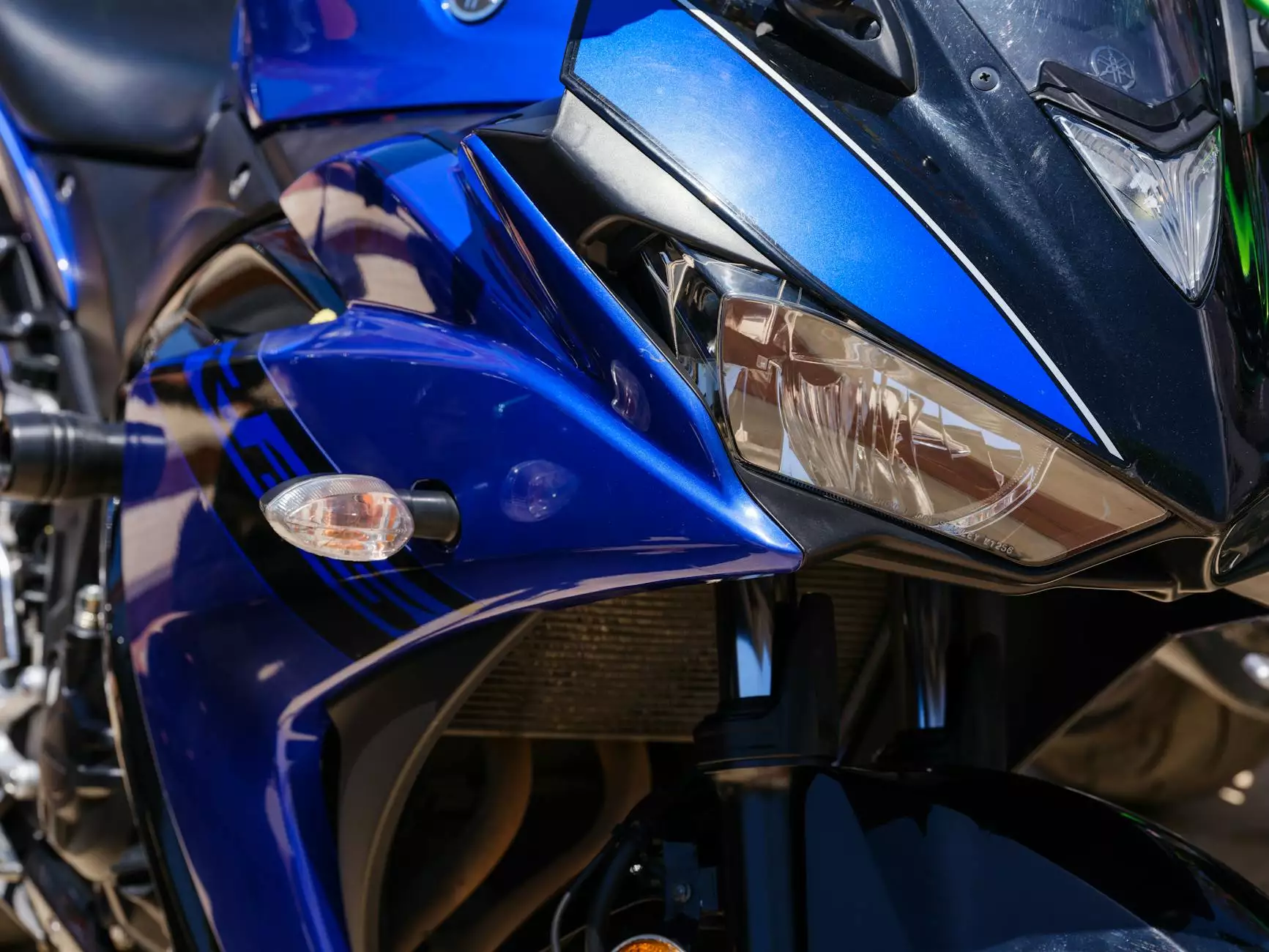
In the fast-paced world of modern business, having the ability to develop products quickly and efficiently is crucial. This is where plastic rapid prototyping shines as a revolutionary technique that has transformed the landscape of product development across various industries. In this comprehensive article, we will explore the myriad benefits of plastic rapid prototyping, illustrate its applications, and explain why it is an essential component for businesses looking to innovate and stay ahead of the competition.
Understanding Plastic Rapid Prototyping
Plastic rapid prototyping encompasses several advanced manufacturing techniques that allow for the quick fabrication of physical models using plastic materials. This process is integral to the development cycle of new products, enabling designers and engineers to create prototypes swiftly and accurately. By employing 3D printing, CNC machining, injection molding, and other cutting-edge technologies, companies can produce prototypes that are not only functional but also aesthetically pleasing.
The Importance of Prototyping in Product Development
Prototyping plays a pivotal role in product development due to several reasons:
- Validation of Concepts: Prototypes allow businesses to validate their design concepts early in the process.
- Cost Efficiency: By identifying issues at the prototype stage, companies can save on manufacturing costs and reduce time spent on modifications.
- User Testing: Prototypes can be used for user feedback, ensuring that the final product meets consumer expectations.
- Iterative Design: The rapid iteration enabled by prototyping fosters creativity and innovation among product teams.
Benefits of Plastic Rapid Prototyping
The adoption of plastic rapid prototyping brings numerous advantages that can significantly enhance business performance:
1. Speed and Efficiency
Speed is the cornerstone of plastic rapid prototyping. Traditional prototyping methods can take weeks or even months to produce a single prototype. In contrast, advanced techniques such as 3D printing can reduce this timeline to just a few hours or days. This acceleration allows teams to iterate more quickly, leading to faster time-to-market for new products.
2. Cost-Effectiveness
By utilizing plastic rapid prototyping, businesses can mitigate costs significantly. The ability to produce low-volume prototypes without the need for expensive tooling makes prototyping accessible to companies of all sizes. Moreover, early identification of design flaws means companies can avoid costly changes during the production phase.
3. Design Flexibility
Prototyping with plastic materials allows for intricate shapes and designs that can be easily modified. This flexibility enables designers to experiment with various aesthetics and functionalities, ensuring that the final product meets all design aspirations.
4. Enhanced Collaboration
With rapid prototyping, teams from different departments can collaborate more effectively. Engineers, designers, and marketing teams can all engage with a tangible product, facilitating better communication and alignment towards achieving common goals.
Applications of Plastic Rapid Prototyping in Various Industries
The versatility of plastic rapid prototyping means that it is applicable across numerous sectors, including:
1. Consumer Products
In the consumer goods industry, rapid prototyping is utilized to create functional prototypes for testing product usability and consumer engagement. From kitchenware to electronics, having a prototype allows for real-world testing of product features.
2. Automotive Industry
Automakers leverage plastic rapid prototyping to develop components such as dashboards, interior trims, and housings. This process not only speeds up development but also enhances the precision and fit of parts.
3. Medical Devices
In the medical field, rapid prototyping is crucial for developing surgical instruments, prosthetics, and diagnostic devices. The ability to produce customized prototypes for patient-specific applications has significantly improved patient care and outcomes.
4. Aerospace
The aerospace sector requires high precision and reliability in its components. Plastic rapid prototyping allows manufacturers to produce lightweight prototypes that are rigorously tested before full-scale production.