Centrifugal Pump: A Key Component in Modern Industries
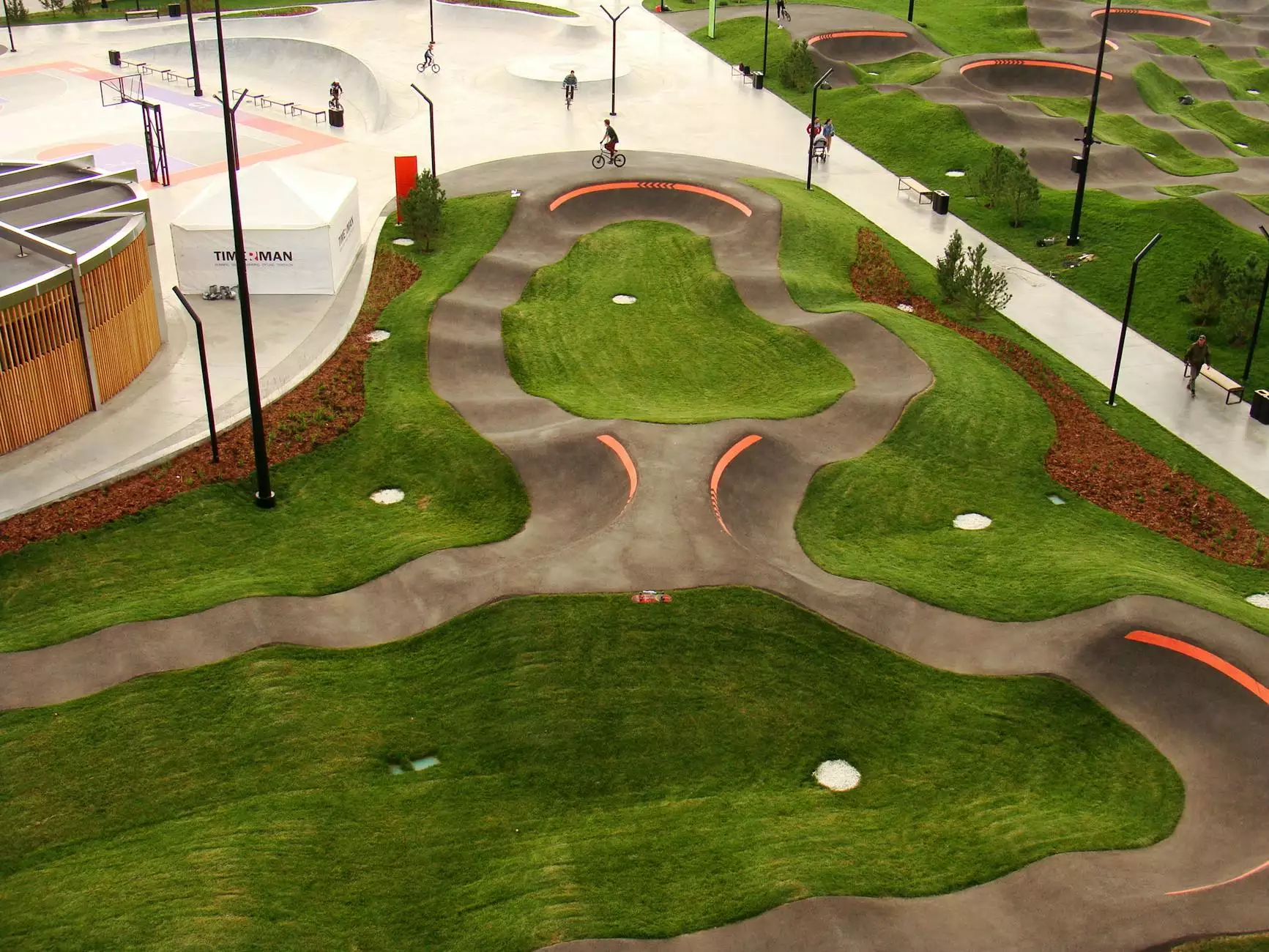
Centrifugal pumps are indispensable tools that facilitate fluid movement in a variety of sectors, including auto repair, farm equipment repair, and structural engineering. This article delves into the intricacies of centrifugal pumps, discussing their mechanics, applications, and benefits across multiple industries.
Understanding Centrifugal Pumps
A centrifugal pump operates on the principle of converting rotational energy into hydrodynamic energy, utilizing an impeller to create kinetic energy that moves fluid through a system. These pumps are particularly favored for their simplicity, efficiency, and versatility in handling different types of fluids.
How Do Centrifugal Pumps Work?
The operation of a centrifugal pump can be broken down into several fundamental steps:
- Fluid Entry: The fluid enters the pump through an inlet and enters the impeller.
- Impeller Action: The impeller spins at high speed, imparting kinetic energy to the fluid.
- Kinetic to Pressure Energy Conversion: As the fluid exits the impeller, its kinetic energy is converted into pressure energy in the volute casing.
- Fluid Discharge: Finally, the fluid is discharged through the outlet, completing the cycle.
The Importance of Centrifugal Pumps in Auto Repair
In the auto repair industry, centrifugal pumps play a crucial role in various applications, including cooling systems, fuel delivery, and oil circulation. Understanding how these pumps fit into automotive maintenance is vital for professionals and enthusiasts alike.
Applications in Automotive Cooling Systems
Automobiles rely on effective cooling systems to maintain optimal engine temperatures. Centrifugal pumps are responsible for circulating coolant fluid throughout the engine block and radiator. The efficiency of these pumps directly affects engine performance and longevity.
Benefits of Using Centrifugal Pumps in Cooling Systems
- High Flow Rates: Centrifugal pumps can adequately circulate coolant at high flow rates, ensuring efficient heat dissipation.
- Compact Size: Their design allows them to be integrated seamlessly into tight engine compartments.
- Reliability: With fewer moving parts than positive displacement pumps, centrifugal pumps typically require less maintenance and offer higher reliability.
Fuel and Oil Circulation
Effective fuel delivery and oil circulation are vital for an automobile's performance. Centrifugal pumps are used in fuel systems to ensure a steady supply of fuel to the engine. In oil lubrication systems, these pumps help maintain pressure, ensuring all engine components receive adequate lubrication.
Key Advantages
- Consistent Pressure: They maintain a consistent pressure of fuel, which enhances engine responsiveness.
- Improved Efficiency: By ensuring optimal oil circulation, centrifugal pumps help in reducing wear and tear on engine components.
The Role of Centrifugal Pumps in Farm Equipment Repair
The agricultural sector heavily relies on centrifugal pumps for irrigation, drainage, and fuel delivery in machinery. These pumps are essential for facilitating efficient operations on farms, enhancing productivity, and ensuring the sustainability of farming practices.
Applications in Irrigation Systems
Farmers depend on centrifugal pumps to move water from sources like wells, rivers, or reservoirs to fields for irrigation. The ability to deliver large volumes of water quickly is crucial during peak growing seasons.
Advantages in Irrigation
- Efficiency: Centrifugal pumps can handle varying flow rates, making them adaptable to different irrigation needs.
- Cost-Effectiveness: These pumps typically consume less energy compared to submersible pumps, reducing operational costs.
Fuel Delivery for Agricultural Equipment
Farm equipment such as tractors and combine harvesters require reliable fuel delivery systems to function efficiently. Centrifugal pumps ensure a steady flow of diesel or biodiesel, aiding in the seamless operation of farming machinery.
Benefits of Efficient Fuel Delivery
- Boosted Productivity: With reliable fuel delivery, equipment downtime is minimized, enhancing overall productivity.
- Sustainability: Ensures the efficient utilization of fuel resources, aligning with sustainable farming practices.
The Application of Centrifugal Pumps in Structural Engineering
Structural engineers utilize centrifugal pumps for various purposes, including concrete mixing, dewatering construction sites, and managing water flow during construction projects. Understanding how these pumps contribute to construction success is vital for engineers and builders.
Concrete Mixing and Delivery
Centrifugal pumps are essential for the effective mixing and delivery of concrete. The capacity to pump thick mixtures with a consistent flow rate aids in achieving the desired strength and durability of concrete structures.
Advantages in Concrete Delivery
- Consistent Mixture: Ensures uniform mixing of concrete components, resulting in a consistent final product.
- Increased Productivity: Significantly reduces the time taken for concrete placement, speeding up construction schedules.
Dewatering Solutions
During construction projects, removing excess water from the site is crucial to maintaining a safe and workable environment. Centrifugal pumps are frequently employed to dewater excavations and trenches, preventing water accumulation.
Benefits of Effective Dewatering
- Safety: Reduces hazards associated with wet ground conditions.
- Compliance: Ensures projects meet local regulations regarding water management on construction sites.
Choosing the Right Centrifugal Pump
When selecting a centrifugal pump for specific applications, several factors must be considered to ensure optimal performance and efficiency. The right choice can significantly impact operational efficiency and cost-effectiveness in any application.
Key Factors to Consider
- Fluid Type: Different pumps are designed to handle varying fluid characteristics, so choose according to the fluid's viscosity and chemical composition.
- Flow Rate: Determine the required flow rate and ensure the pump can meet those needs without excessive energy consumption.
- Head Pressure: Assess the vertical distance the pump must move the fluid, considering the system's total dynamic head.
- Material Construction: Select a pump made from materials resistant to corrosion or wear, based on the fluid being pumped.
Maintenance and Care of Centrifugal Pumps
To ensure longevity and optimal performance, regular maintenance of centrifugal pumps is essential. Proper care can prevent costly repairs and downtime.
Regular Inspection
Conducting regular inspections helps identify potential issues early. Look for signs of wear, leaks, or unusual sounds during operation.
Routine Cleaning
Keeping the pump and surrounding area clean can prevent clogging and ensure smooth operation. This includes checking and cleaning the filter regularly.
Lubrication
Ensure that moving parts are adequately lubricated according to the manufacturer's recommendations to reduce friction and wear.
Conclusion: The Versatility of Centrifugal Pumps
In summary, centrifugal pumps are vital components across many industries, including auto repair, farm equipment repair, and structural engineering. Their efficiency, reliability, and versatility make them an essential tool for professionals seeking to optimize their operations. Understanding their functionality and applications can lead to improved performance and greater innovation within these fields.
For more information and expert services related to centrifugal pumps and their applications, visit Michael Smith Engineers. Our team of professionals is dedicated to providing top-notch solutions tailored to your business needs.