Revolutionizing Construction with Automatic Inspection Systems
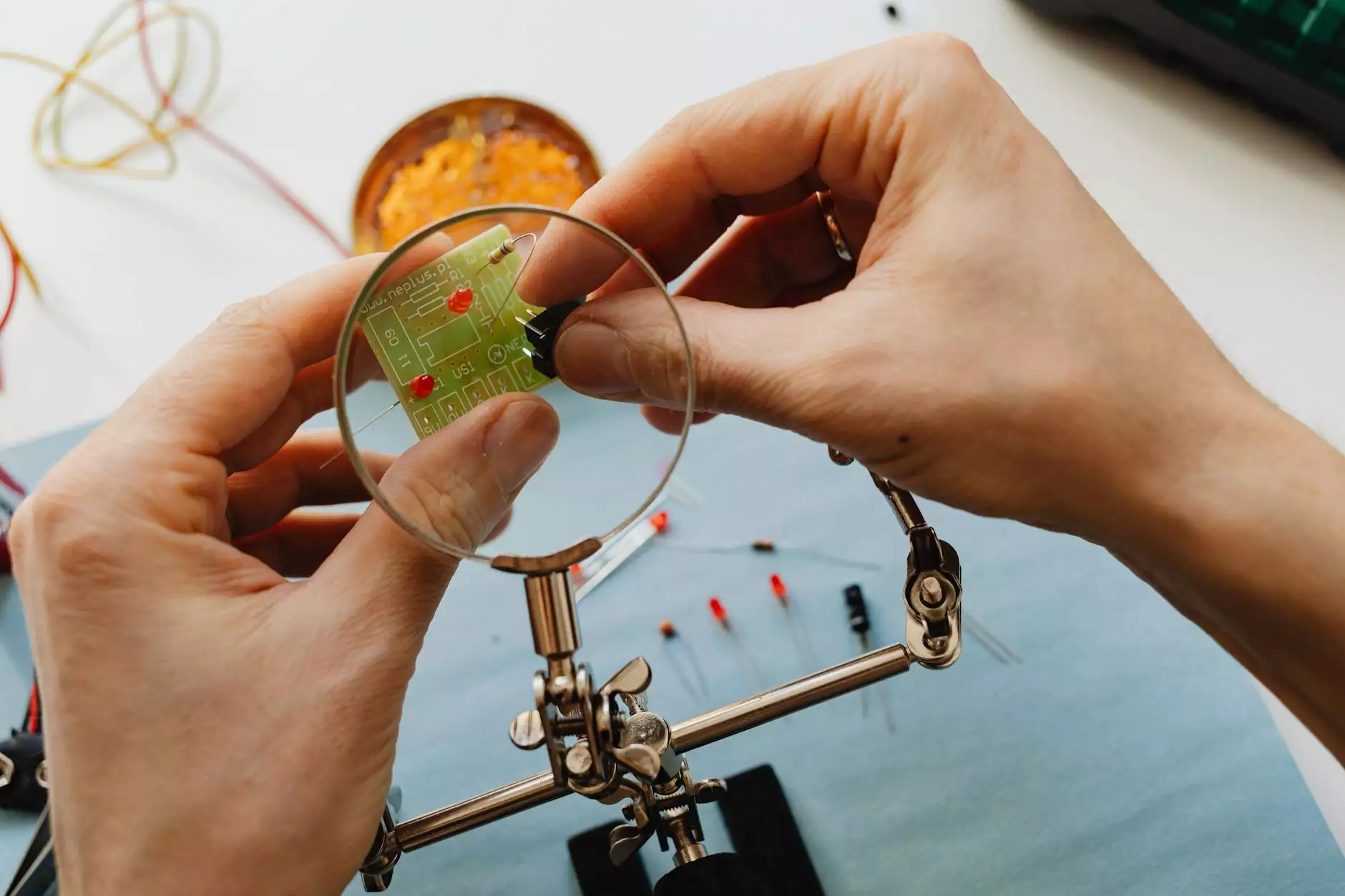
Introduction to Automatic Inspection Systems
The construction industry has witnessed significant transformations in recent years, with technology playing a pivotal role. One of the most impactful advancements is the development of the automatic inspection system for construction. These systems offer a myriad of benefits, enhancing the efficiency and safety of construction processes.
What is an Automatic Inspection System?
An automatic inspection system in construction refers to a technology solution that automates various aspects of the inspection process. Utilizing advanced sensors, cameras, and AI algorithms, these systems can perform real-time monitoring and evaluation of construction activities, ensuring compliance with regulations and quality standards.
Benefits of Automatic Inspection Systems
Implementing an automatic inspection system for construction brings multiple benefits, including:
- Enhanced Accuracy: Automated systems minimize human error, providing precise measurements and evaluations.
- Increased Efficiency: Fast inspections allow for quicker project completion and reduced downtime.
- Cost Reduction: By reducing the need for rework and manual inspections, overall project costs can decrease significantly.
- Safety Assurance: Continuous monitoring enhances safety measures, helping to prevent accidents on-site.
- Regulatory Compliance: Automatic systems ensure that all inspections meet the necessary legal standards, reducing the risk of violations.
How Automatic Inspection Systems Work
The operation of an automatic inspection system for construction typically involves several key steps:
- Data Collection: The system utilizes various sensors and imaging technologies to collect data about the construction site.
- Data Analysis: Collected data is analyzed using machine learning algorithms to identify potential issues or discrepancies.
- Reporting: The system generates comprehensive reports that detail findings and recommendations for improvements.
- Continuous Monitoring: Ongoing assessments ensure that any new issues are promptly addressed, maintaining a high standard throughout the project's lifecycle.
Common Applications in Construction
Automatic inspection systems are versatile and can be used in various aspects of the construction process, including:
1. Structural Integrity Assessment
Continuous monitoring of structures during and after construction helps identify weak points or deviations from planned specifications.
2. Compliance Checks
Automatic systems verify that all construction activities meet local regulations and industry standards, reducing legal risks.
3. Material Quality Control
Inspection systems ensure that all materials used in construction are of the required quality, which is essential for durability and safety.
4. Workflow Efficiency
By streamlining inspection processes, these systems contribute to overall project efficiency, allowing for better time and resource management.
Case Studies: Success Stories
Numerous construction companies have successfully integrated automatic inspection systems, leading to improved outcomes. Here are a few notable examples:
Case Study 1: Major Urban Development Project
In a recent urban development project, the integration of an automatic inspection system reduced inspection times by 30% and identified defects that could have gone unnoticed. This proactive approach saved the company approximately $500,000 in potential rework costs.
Case Study 2: High-Rise Building Construction
During the construction of a 250-unit high-rise, the use of automated inspection allowed for continual monitoring of structural elements. This results-driven strategy ensured that the project finished two months ahead of schedule, proving the efficacy of technology in maintaining deadlines.
Choosing the Right System for Your Needs
When considering the implementation of an automatic inspection system for construction, several factors should be evaluated:
- Project Size and Complexity: Larger projects may require more sophisticated systems to handle various inspection needs.
- Integration with Existing Processes: Ensure that the new system can seamlessly integrate with current project management tools and workflows.
- Budget Constraints: Analyze the cost versus benefit of the inspection system to ensure it aligns with your financial objectives.
- Technical Support and Training: Choose a provider that offers robust support and comprehensive training for your team.
The Future of Inspection in Construction
The landscape of the construction industry is continually evolving, with automatic inspection systems taking center stage. As AI and IoT technologies advance, we can expect even more innovative solutions that will transform how inspections are conducted. Key trends to watch include:
- Increased Automation: Future systems will automate more complex inspection tasks, making them even more efficient.
- Integration of Drones: Drones will play a greater role in site inspections, providing aerial views and real-time data collection.
- Data Analytics: Enhanced data analytics capabilities will enable better decision-making based on trends and patterns identified through inspections.
- Sustainability Focus: Future systems will prioritize sustainability, ensuring that inspections adhere to eco-friendly practices and regulations.
Conclusion
The integration of automatic inspection systems for construction is revolutionizing the industry, offering unlimited potential for efficiency, safety, and quality assurance. As the construction sector embraces these innovative technologies, the possibilities for enhanced project management continue to expand. Companies like Intalio, offering services such as content management, business process automation, and data governance systems, are at the forefront of this transformation, helping businesses to navigate the complexities of modern construction with confidence and agility.